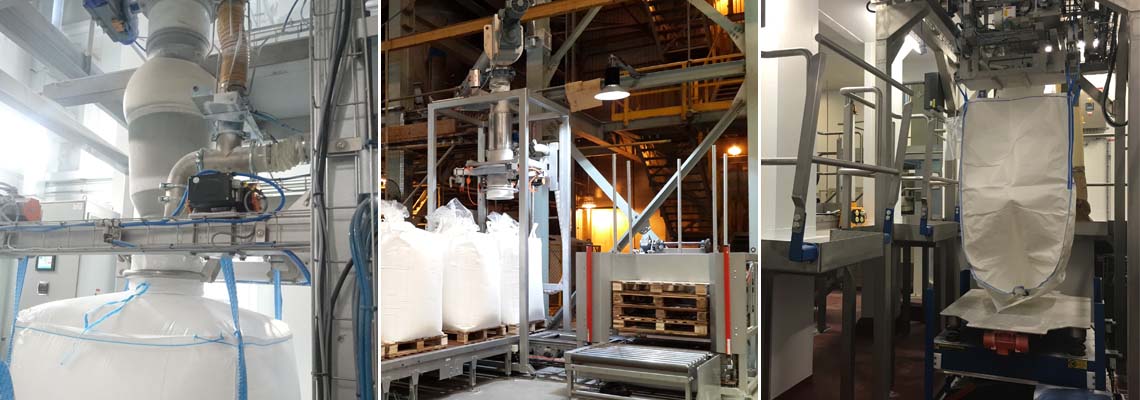
Dans la plupart des applications industrielles, deux raisons principales motivent une usine à investir dans une station de remplissage de big bags automatisée :
- Minimiser l'intervention des opérateurs
- Répondre à une augmentation de la demande de produits/des objectifs de rendement
Quels sont les différents équipements pour la mise en œuvre d'un système de remplissage de big bags à haut débit ?
1. Trémie tampon pesée
Les trémies tampons pesées qui alimentent les ensacheuses de big bags constituent un des composants les plus importants sur les systèmes à haut débit. Ces réservoirs de poudres sont utilisés pour stocker de manière temporaire les poudres et les granulés afin d'assurer une alimentation précise et contrôlée des process de production.
Les composants les plus couramment utilisés sur les trémies tampon pesées sont les sondes de niveau haut, les sondes de niveau bas et les cellules de charge (également nommées pesons). Les sondes de niveau permettent d'indiquer à l’équipement en amont le niveau de remplissage de la trémie et ainsi activer le remplissage ou la vidange de celle-ci.
Afin d'obtenir de façon automatique un poids de remplissage précis dans les big bags situés en aval, des cellules de charge sont installées sous les supports de la trémie. Ces pesons sont généralement utilisés dans les systèmes qui utilisent la fonction “gain de poids” ou “perte de poids”.
Les cellules de charge indiquent au système de commande que le poids cible de poudre a été atteint dans la trémie. Lorsqu’il s’agit d’un système de remplissage de big bags automatique qui exige des taux de conditionnement en big bags élevés, les trémies tampon à double gain de poids fonctionneront de manière séquentielle.
Lorsque des trémies tampon à gain de poids sont installées à proximité les unes des autres et alimentent la même station de remplissage de big bags, la première trémie contenant la poudre peut se décharger dans le big bag pendant que la seconde trémie est en cours de remplissage. En travaillant de cette manière en temps masqué, il y a toujours une trémie pleine prête à remplir un big bag.
Les trémies tampon pesées sont généralement dimensionnées en fonction de la densité en vrac de la poudre manutentionnée et de la capacité du big bag à remplir. Des vannes papillon ou des vannes guillotine sont installées en sortie de trémie pour contrôler le débit de la poudre.
D'autres composants peuvent compléter l’installation. En effet, des dispositifs d'aide à l'écoulement tels que des moteurs vibrants, des buses à jet d'air, des marteaux pneumatiques, etc. aident à prévenir les problèmes de mottes ou de pontage lorsqu’il s’agit de poudres qui ont tendance à s’écouler difficilement.
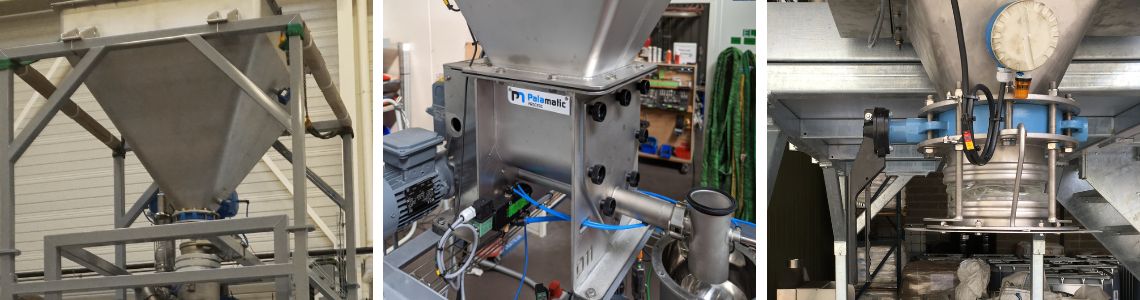
2. Équipements de contrôle du débit et de dosage des poudres
Un autre élément essentiel pour obtenir un taux de remplissage élevé des big bags est la façon dont la poudre est manipulée et dosée une fois qu'elle a quitté la trémie d'alimentation en amont.
Comme indiqué précédemment, une vanne papillon ou une vanne à guillotine est généralement utilisée comme vanne principale de contrôle du débit de la poudre en sortie de trémie.
À partir de ce point, alors que la poudre s'écoule dans une goulotte de connexion par gravité vers la station de remplissage située en dessous, elle peut être dirigée vers l'un des deux conduits.
Le conduit principal est le conduit à haut débit. Il est souvent complété par des vannes papillon juste au-dessus et au-dessous des voies.
Lorsque le big bag est rempli à 95% de sa capacité totale, la vanne papillon située en haut du conduit à haut débit se ferme et détourne la poudre vers le doseur à vis. Le doseur à vis permet un dosage des poudres avec une précision répétable. Il est composé d’une trémie intégrée avec un agitateur qui alimente un tube. À l'intérieur du tube, se trouve une petite vis qui pousse le produit vers l’extrémité de sortie en direction du process en aval. Ces doseurs à vis offrent une bonne précision de dosage qui peut atteindre -/+ 1-2 grammes.
Un autre type de système de dosage de poudre qui peut être utilisé est le doseur vibrant. Les doseurs vibrants utilisent des moteurs à vibration et la structure est soutenue par des ressorts qui permettent à l'unité de vibrer. L'auge présente une pente minimale qui permet à l'unité de déplacer le matériau vers l'extrémité du plateau pour alimenter le processus en aval.
Le taux d'alimentation peut être contrôlé en augmentant ou en diminuant l'amplitude et la fréquence des vibrations. Ce type de dispositif d'alimentation en poudre permet de préserver l'intégrité du produit ou d'éviter une usure inutile dans le cas de matériaux abrasifs. Le doseur à vis se met en fonctionnement pour les derniers 5% de la cible de remplissage du big bag. En utilisant un dispositif d'alimentation fractionné comme celui décrit ci-dessus, les systèmes de remplissage automatisés peuvent remplir rapidement et efficacement les big bags avec précision.
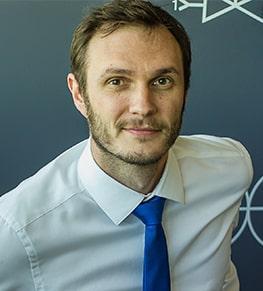
Vous cherchez une station big bag ? Je suis
disponible pour vous conseiller dans votre étude.
Jean-Luc, expert poudre
3. Confinement et contrôle des poussières
L'une des pièces d'équipement les plus indispensables pour toute installation de production industrielle est le dépoussiérage et la filtration. Il est également primordial que tous les équipements de manutention soient conçus pour fonctionner de manière étanche à la poussière et contenir les poudres manipulées. En effet, les risques sont importants : toxicité du matériau et exposition aux opérateurs, accidents par glissade et chute dus à la présence de poudre et de poussière au sol, défaillance mécanique de l'équipement, rapport du mélange air/poussière entraînant une explosion etc…
Il existe plusieurs types de dépoussiéreurs à envisager :
- Les systèmes de dépoussiérage centralisés pour tous les équipements de production. Cela comprend les filtres à manches en tissu, les séparateurs inertiels (comme les cyclones mécaniques), les filtres humides, les collecteurs à cartouches et les filtres électrostatiques
- Les unités de filtres à poussières intégrées spécifiques à l'équipement : filtre à poussière intégré sur le dessus d'une station de vidange des sacs par exemple
- Les filtres de dégazage
- Les hottes aspirantes
- Les anneaux de dépoussiérage (anneaux de Pouyes) : sur le dessus d'un réservoir de stockage par exemple où les opérateurs alimentent manuellement les sacs de poudre.
Les unités de dépoussiérage sont généralement équipées de cartouches filtrantes montées sur le côté ou sur le dessus. Ces filtres sont reliés à un réservoir d'air comprimé externe réglé sur un cycle de minuterie. Lorsque la poussière passe à travers le filtre, un jet d'air intermittent est envoyé depuis le côté opposé afin de nettoyer l'accumulation excessive de poussière. Ce système de nettoyage par impulsions à jet inversé a deux fonctions : 1. Il empêche les filtres de se colmater sans nécessiter d'entretien
2. Il aide à récupérer le produit échappé dans les filtres.
Pour le remplissage des big bags, il est important que la connexion entre la tête de remplissage et la goulotte du big bag soit sécurisée et étanche à la poussière.
La méthode la plus courante consiste à utiliser un joint gonflant sur la tête de remplissage. L'opérateur positionne la goulotte du big bag autour du joint en élastomère. De l'air sous pression est introduit dans le joint, ce qui le fait gonfler et permet un maintien ferme de la goulotte.
La tête de remplissage peut également se présenter avec une double enveloppe (un tube intérieur entouré d'un tube extérieur). Le canal intérieur permet le passage de la poudre et le remplissage du big bag. Le canal extérieur permet à l'air et aux poussières très légères de s'échapper par une pièce de raccordement. Ce piquage peut être équipé d'une manchette filtrante ou d'un tuyau qui se connecte à un dépoussiéreur centralisé. Dans les unités de production qui traitent des matériaux particulièrement toxiques, comme par exemple les poudres de lithium dans l'industrie de fabrication des batteries, l'ensemble de l'installation peut être installé dans une enceinte conçue pour tirer un vide atmosphérique constant vers un système de dépoussiérage extérieur.
4. Table vibrante de densification et pesons
L'un des problèmes les plus courants lors du transport et du stockage de big bags remplis de poudres et de matériaux granulaires est celui du manque de stabilité. Ce phénomène est du au fait que les particules de poudre sont trop “aérées” pendant l'opération de remplissage.
Lorsque le matériau se dépose gravitairement de lui-même, une séparation des particules peut apparaitre. De ce fait, les particules fines tombent au fond et les particules plus grosses restent sur le dessus.
Le big bag peut alors s'affaisser et basculer sur le côté, ce qui entraîne une forte instabilité lors de son déplacement ou de son empilage pendant les phases de stockage.
Les tables vibrantes de densification sont un composant nécessaire de toute ligne de production de remplissage de big bags semi-automatique ou entièrement automatisée.
Au fur et à mesure que le sac en vrac se remplit de matériau en vrac, la table de densification vibre par intermittence. Cette vibration permet aux petites poches d'air entre les particules de s'échapper, ce qui permet de resserrer les particules entre elles. Ainsi, la ségrégation des particules est limitée et le big bag est plus rigide, donc plus facilement transportable et stockable.
Aussi, l'installation d'un capteur de force sur cette table vibrante convertit une force telle que la tension, la compression, la pression ou le couple en un signal électrique qui peut être mesuré et normalisé. Lorsque la force appliquée à la cellule de charge augmente, le signal électrique change en conséquence.
Les cellules de charge ou pesons sont connectés à un automate programmable (PLC) qui lit la quantité de poids qui entre dans un big bag pendant la séquence de remplissage.
Un poids cible est programmé sur le pupitre de commande. Lorsque les pesons indiquent que le big bag est presque complètement rempli, l'automate envoie un signal à l'unité de dosage de la poudre (alimentateur à vis, vanne rotative) pour ralentir la cadence et verser les derniers 5% du poids cible.
Lorsque le poids cible est atteint, les cellules de charge envoient un signal à l'automate qui indique à la vanne de se fermer et d'arrêter le remplissage. En utilisant des pesons, nous pouvons automatiser la séquence de remplissage sans l'intervention d'un opérateur et ainsi obtenir un poids de remplissage très précis.
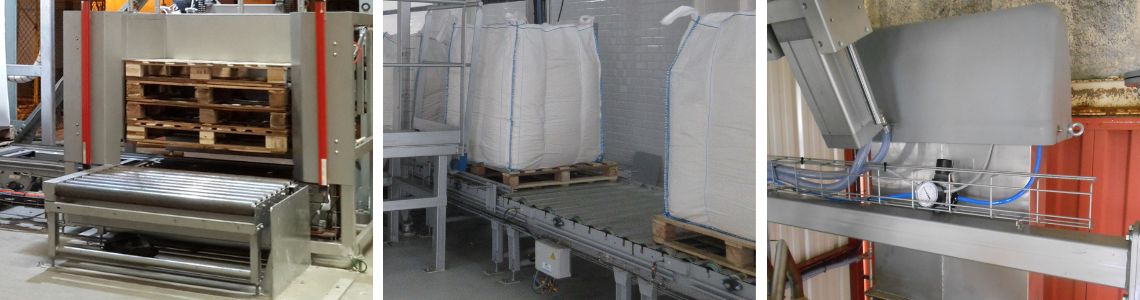
5. Dépileur de palettes et convoyeur à rouleaux mécanique
Les deux dernières composantes essentielles pour automatiser votre ligne de remplissage de conteneurs souples sont les dépileurs et les convoyeurs à rouleaux mécaniques.
Les dépileurs de palettes utilisent des bras d'indexation robotisés reliés à des cylindres pneumatiques qui peuvent lever, baisser et positionner une palette sur une station de remplissage.
Ils peuvent contenir jusqu'à 20 palettes à la fois. La machine alimente une palette toutes les 35 secondes et peut être conçue pour s'adapter à différentes dimensions de palettes. Chaque fois qu'un big bag a fini d'être rempli, l'automate programmable peut indiquer au dépileur de palettes de positionner la palette suivante sur le convoyeur à rouleaux mécanique.
Les convoyeurs à rouleaux mécaniques ont plusieurs fonctions différentes mais sont principalement utilisés dans ce cas pour transférer les palettes vers la station de remplissage, puis ensuite évacuer le big bag plein vers une zone de stockage tampon. Un opérateur vient alors récupérer le big bag plein à l’aide d’un chariot élévateur pour le transporter vers la zone de stockage définitive. Tous les paramètres et les séquences sont contrôlés par l'automate programmable, ce qui élimine tout travail manuel. Les rouleaux du convoyeur sont espacés de manière égale et sont entraînés par un moteur à engrenages situé latéralement, ou par gravité sur un angle d'inclinaison minimal. Les convoyeurs à rouleaux par gravité comportent des rouleaux régulateurs de vitesse qui servent à contrôler la vitesse de la charge transportée, comme un big bag sur sa palette dans notre cas. Quel que soit le type de convoyeur, ils fonctionnent en séquence pour fournir un débit constant des big bags vers et à partir de la station de remplissage.
Grâce à ces dispositifs, les opérations de remplissage de big bags réduisent au minimum le nombre d’opérateurs sur un même poste de travail.