Optimiser la fluidité des poudres en hydrométallurgie : enjeux, bonnes pratiques et cas d'application industrielle
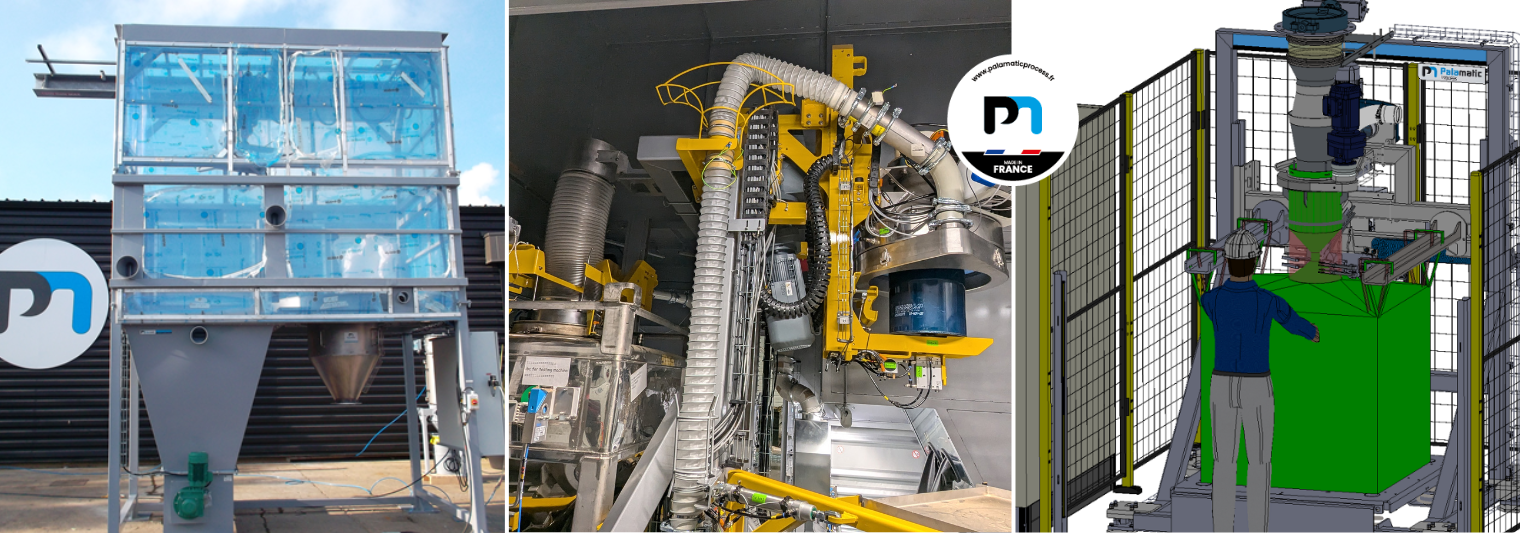
Dans l'industrie hydrométallurgique moderne, la maîtrise des propriétés d'écoulement des poudres représente un enjeu technique et économique majeur.
Les procédés hydrométallurgiques impliquent la manipulation de matières pulvérulentes à de nombreuses étapes : broyage des minerais, manipulation des précipités, filtration, séchage et conditionnement des produits finis.
Une fluidité inadéquate des poudres transforme rapidement une installation performante en cauchemar opérationnel : engorgements des silos, formation de voûtes, ségrégation des particules et colmatage des équipements.
Cet article propose un tour d'horizon complet des enjeux, méthodes et innovations permettant d'améliorer durablement la fluidité des poudres dans les procédés hydrométallurgiques.
1. Les enjeux techniques et économiques d'une mauvaise fluidité des poudres
Impact sur les coûts de maintenance
La manipulation de poudres à faible fluidité entraîne une usure prématurée des équipements de transfert.
Les problèmes d'écoulement sont responsables de 35 à 40% des interventions de maintenance non-programmées dans les unités hydrométallurgiques.
Une étude menée en 2023 sur quinze sites de production a démontré qu'une amélioration de l'indice de fluidité des poudres (mesuré par l'angle de repos) de seulement 5° peut réduire les coûts de maintenance associés de 22% en moyenne.
Les composants les plus affectés sont généralement :
- Les vis sans fin et transporteurs, dont la durée de vie peut être réduite de 30 à 50%
- Les vannes et clapets, qui subissent une abrasion accélérée
- Les revêtements intérieurs des silos et trémies, détériorés par les efforts excessifs
Ces défaillances récurrentes conduisent à des dépenses directes (remplacement de pièces, main d'œuvre) estimées entre 2 et 4% du chiffre d'affaires annuel selon la taille des installations.
Pertes de production associées
Les perturbations d'écoulement engendrent des arrêts de production particulièrement préjudiciables.
Une analyse comparative menée sur le secteur hydrométallurgique canadien en 2022 a révélé que les problèmes de fluidité des poudres étaient responsables de :
- 7 à 12% des temps d'arrêt imprévus
- 3 à 5% de réduction du taux d'utilisation global des capacités
- Un manque à gagner moyen de 850€ par tonne de capacité installée et par an
Dans les unités de lixiviation où la régularité d'alimentation en réactifs solides est critique, les fluctuations d'écoulement peuvent réduire les rendements d'extraction métallique de 3 à 8 points, impactant directement la rentabilité.
Incidence sur la qualité des produits
La qualité des produits est fortement tributaire d'un écoulement homogène et contrôlé des poudres.
Les anomalies d'écoulement induisent :
- Des phénomènes de ségrégation : Les particules de tailles ou densités différentes tendent à se séparer lors de l'écoulement, créant des hétérogénéités dans les mélanges.
Dans les procédés de précipitation sélective, cette ségrégation peut induire des variations de pureté du produit final de l'ordre de 0,5 à 2%.
- Des irrégularités de dosage : Un écoulement erratique conduit à des fluctuations de débit pouvant atteindre ±15% autour de la valeur nominale, compromettant la stœchiométrie des réactions et affectant le rendement global.
- Des modifications de propriétés physiques : Les contraintes mécaniques excessives appliquées peuvent altérer la structure cristalline et la morphologie des particules.
Une étude sur les poudres d'oxyde de zinc a démontré que les contraintes de cisaillement élevées pouvaient réduire la surface spécifique jusqu'à 18%, affectant directement la réactivité du produit.
Les non-conformités résultant de ces problèmes représentent en moyenne 2,8% de la production totale dans le secteur.
Risques pour la sécurité industrielle
Les risques liés à une mauvaise fluidité des poudres concernent également la sécurité :
Les risques liés à une mauvaise fluidité peuvent inclure :
- Risque d'effondrement de voûtes : La formation de ponts et voûtes dans les silos crée des zones de vide qui peuvent s'effondrer brutalement, générant des surcharges instantanées.
- Émissions de poussières : Les interventions manuelles pour débloquer les écoulements provoquent des émissions de poussières potentiellement toxiques, représentant un risque d'exposition professionnelle significatif.
- Surcharges mécaniques : Les efforts déployés pour rétablir l'écoulement peuvent soumettre les structures à des contraintes excédant leurs limites de conception.
Les statistiques sectorielles indiquent que 12% des accidents industriels graves dans le domaine hydrométallurgique sont liés à des problèmes d'écoulement de matières solides.
L'analyse des incidents montre que le temps d'exposition des opérateurs aux risques liés aux interventions sur poudres bloquées peut être réduit de 78% par l'amélioration préventive de la fluidité des matériaux.
2. Optimisation de la granulométrie et de la morphologie des particules
Mécanisme d'action
La distribution granulométrique et la forme des particules influencent directement les interactions interparticulaires et donc la fluidité globale.
L'optimisation consiste à :
- Ajuster la répartition des tailles de particules pour minimiser les espaces interstitiels tout en limitant les forces de cohésion
- Favoriser des morphologies sphériques ou ellipsoïdales qui réduisent les blocages mécaniques et les surfaces de contact
Ces modifications agissent directement sur le coefficient de frottement interne et l'angle de talus naturel, paramètres déterminants de la fluidité.
Avantages et limites
Avantages :
- Solution pérenne ne nécessitant pas d'additifs chimiques
- Amélioration simultanée de la compacité et de la fluidité
- Réduction significative des phénomènes de voûtage (jusqu'à 65% selon les cas étudiés)
Limites :
- Nécessite des équipements de broyage/tamisage précis et bien entretenus
- Peut modifier d'autres propriétés physicochimiques du matériau (réactivité, solubilité)
- Investissement initial souvent conséquent
Exemple industriel
La raffinerie hydrométallurgique de Kokkola (Finlande) a optimisé la granulométrie de son hydroxyde de zinc précipité en adoptant un système de classification pneumatique à double étage.
La distribution granulométrique resserrée (90% des particules entre 45 et 75 μm) a permis une amélioration de l'indice d'écoulement Hausner de 1,38 à 1,22.
Résultats obtenus :
- Réduction de 82% des interventions pour déblocage
- Augmentation de 7,3% du débit massique dans les systèmes de transfert
- Retour sur investissement atteint en 8,5 mois d'exploitation
- Économie annuelle estimée à 420 000€
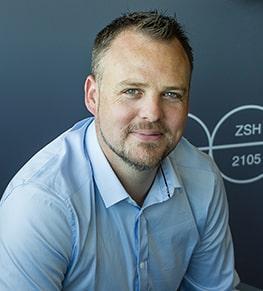
Vous avez un projet ?
Je suis disponible pour vous conseiller et vous accompagner dans votre étude.
Erwan, expert en confinement de poudres
3. Solutions opérationnelles pour améliorer la fluidité des poudres
Ajouts d'additifs fluidifiants
Mécanisme d'action
Les additifs fluidifiants agissent selon trois mécanismes principaux :
- Réduction des forces électrostatiques par neutralisation des charges de surface
- Diminution des forces de Van der Waals par modification de la rugosité superficielle
- Création d'une couche limite réduisant les contacts directs entre particules
Les additifs les plus couramment utilisés en hydrométallurgie sont la silice pyrogénée (0,1-0,5%), les stéarates métalliques (0,2-1%) et certains dérivés organiques comme le polyéthylène glycol (0,3-0,8%).
Avantages et limites
Avantages :
- Mise en œuvre rapide sans modification majeure des équipements
- Dosage ajustable en fonction des conditions d'exploitation
- Efficacité élevée même à faible concentration (typiquement <1%)
Limites :
- Coût récurrent lié à la consommation d'additifs
- Risque de contamination du produit final
- Compatibilité parfois limitée avec les étapes ultérieures du procédé
Exemple industriel
Dans une unité de production d'oxyde de cuivre à partir de lixiviats au Chili, l'incorporation de 0,3% de silice pyrogénée hydrophobe dans la poudre d'oxyde après filtration a permis :
- Une réduction de l'angle de repos dynamique de 56° à 38°
- Une diminution de 91% des blocages dans les systèmes d'ensachage
- Une amélioration de la précision de dosage de ±12% à ±3%
- Un surcoût matière de 1,2€/tonne compensé par une réduction des coûts opérationnels de 3,8€/tonne
L'utilisation d'un additif biosourcé à base d'amidon modifié (0,4%) a montré une efficacité comparable avec un impact environnemental réduit de 43% selon l'analyse du cycle de vie.
Traitements mécaniques spécifiques
Mécanisme d'action
Les traitements mécaniques visent à perturber les forces cohésives entre particules et à fournir l'énergie nécessaire pour initier et maintenir l'écoulement.
Trois approches principales sont déployées :
- Vibration contrôlée : Application de vibrations de fréquence et amplitude optimisées pour fluidiser temporairement la masse de poudre sans induire de compaction.
- Fluidisation mécanique : Utilisation d'agitateurs, mélangeurs ou disques rotatifs créant un cisaillement contrôlé qui maintient la poudre dans un état quasi-fluide.
- Assistance pneumatique : Injection d'air à faible pression pour réduire les contacts interparticulaires et faciliter l'écoulement.
Avantages et limites
Avantages :
- Action immédiate sur l'écoulement
- Adaptabilité aux variations de propriétés des matériaux
- Conservation des caractéristiques physicochimiques de la poudre
Limites :
- Consommation énergétique parfois importante
- Possible attrition des particules fragiles
- Nécessité d'une conception spécifique pour chaque installation
Exemple industriel
La société Umicore a implémenté un système de fluidisation mécanique par cône vibrant dans son unité de traitement des boues anodiques de Hoboken (Belgique).
Le système combine une vibration basse fréquence (12 Hz) avec une injection d'air pulsé synchronisée.
Les résultats mesurés sont éloquents :
- Augmentation du débit d'écoulement de 760 kg/h à 1250 kg/h (+64%)
- Réduction de la variabilité du débit de ±18% à ±4%
- Diminution de la puissance consommée par tonne transférée de 1,8 kWh à 1,2 kWh
- Élimination complète des interventions manuelles pour déblocage
L'investissement de 175 000€ a été amorti en moins de 14 mois grâce aux gains de productivité et à la réduction des coûts de maintenance.
Modifications des conditions environnementales
Mécanisme d'action
Les propriétés d'écoulement des poudres sont fortement influencées par les conditions ambiantes :
- Contrôle de l'humidité relative : La réduction de l'humidité limite la formation de ponts liquides entre particules, phénomène particulièrement problématique pour les sels hygrométriques.
- Gestion de la température : L'augmentation contrôlée de la température réduit l'adsorption d'humidité et peut diminuer les forces d'adhésion entre particules.
- Modification de la pression : Dans certains cas, une légère pressurisation ou dépressurisation peut améliorer significativement les caractéristiques d'écoulement.
Avantages et limites
Avantages :
- Amélioration uniforme des propriétés d'écoulement
- Absence d'altération chimique des produits
- Synergie possible avec d'autres méthodes d'optimisation
Limites :
- Coûts énergétiques associés au conditionnement d'air
- Complexité technique des systèmes de contrôle environnemental
- Sensibilité aux variations saisonnières
Exemple industriel
Une usine de production de sulfate de nickel en Australie a mis en place un système intégré de contrôle environnemental pour ses unités de séchage et conditionnement.
Le système maintient une humidité relative inférieure à 35% et une température constante de 33°C dans les zones critiques de transfert de poudre.
Les résultats documentés après 12 mois d'exploitation sont significatifs :
- Amélioration de l'indice de coulabilité Carr de 22 à 16
- Réduction de 68% des incidents d'écoulement
- Diminution des pertes de produit liées aux manipulations de 2,3% à 0,8%
- Consommation énergétique additionnelle de 135 kWh/tonne compensée par une augmentation de productivité de 11%
4. Innovations technologiques récentes et perspectives d'avenir
Revêtements nano-structurés
Des revêtements polymères ou céramiques à échelle nanométrique sont désormais appliqués sur les surfaces en contact avec les poudres.
Ces traitements créent des motifs superficiels optimisés (type "peau de requin") qui réduisent drastiquement l'adhérence des particules.
Les essais industriels montrent une réduction de l'angle de friction de 30 à 40% par rapport aux surfaces conventionnelles polies.
La durabilité de ces revêtements atteint maintenant 18 à 24 mois en environnement abrasif.
Systèmes de caractérisation en ligne
La rhéologie des poudres peut désormais être surveillée en continu grâce à des capteurs acoustiques et optiques non-intrusifs.
Ces dispositifs analysent en temps réel :
- La distribution granulométrique
- La cohésion interparticulaire
- Les tendances à l'agglomération
Couplés à des algorithmes d'intelligence artificielle, ces systèmes permettent d'anticiper les problèmes d'écoulement et d'ajuster automatiquement les paramètres opératoires avant l'apparition de blocages.
Fluidisation électrostatique contrôlée
Une approche innovante consiste à appliquer un champ électrostatique modulé qui modifie les forces de cohésion entre particules.
Les prototypes actuels permettent de réduire jusqu'à 60% les forces d'adhésion sans modification chimique de la poudre.
Cette technologie encore en phase de démonstration industrielle semble particulièrement prometteuse pour les poudres métalliques fines et les oxydes semi-conducteurs.
Bio-additifs issus de l'économie circulaire
La recherche récente a identifié plusieurs sous-produits agricoles et forestiers qui, après traitement spécifique, présentent d'excellentes propriétés fluidifiantes.
Ces additifs biosourcés offrent une alternative durable aux agents de fluidité synthétiques avec un impact environnemental réduit de 70 à 85%.
Les dérivés de lignine modifiée et les nanofibrilles de cellulose montrent des performances comparables aux silices pyrogénées conventionnelles à concentration équivalente.
Conclusion
Conclusion
L'optimisation de la fluidité des poudres constitue un levier de performance crucial pour l'industrie hydrométallurgique.
Pour les industriels souhaitant améliorer leurs procédés, nous recommandons :
- Caractériser précisément les propriétés d'écoulement des poudres à chaque étape critique du procédé
- Développer une stratégie intégrée combinant optimisation granulométrique, additifs et assistance mécanique adaptée
- Installer des systèmes de monitoring permettant de détecter précocement les dérives et d'intervenir préventivement
- Former les équipes opérationnelles aux fondamentaux de la mécanique des poudres
- Intégrer la fluidité comme paramètre clé dans la démarche d'amélioration continue
Les retours sur investissement, généralement inférieurs à 18 mois, combinés à l'amélioration des conditions de travail et de la qualité des produits, justifient pleinement l'attention croissante portée à cette problématique par les leaders du secteur hydrométallurgique.
📞 Vous travaillez dans le traitement ou la valorisation de l'hydrométallurgie ?
Contactez nos experts pour concevoir ensemble une ligne de production sur-mesure, performante et sécurisée.