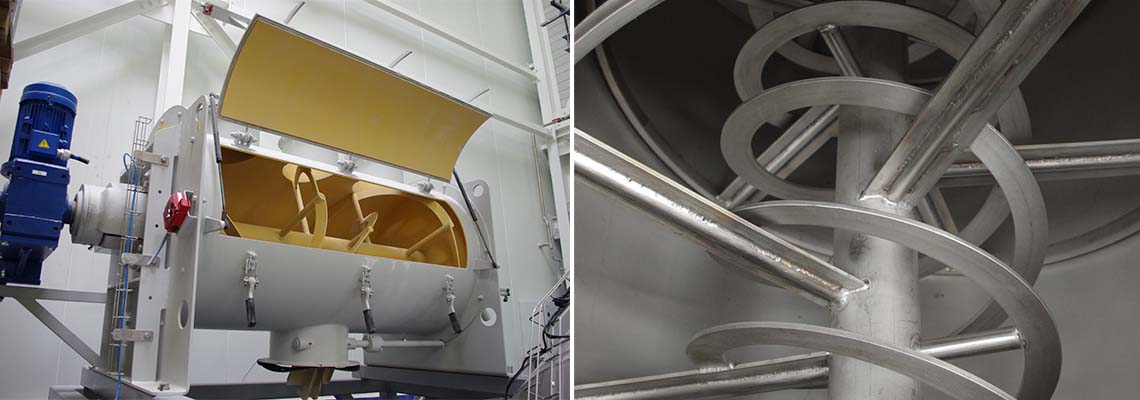
1. Principe de fonctionnement du mélangeur à ruban
Les mélangeurs à ruban sont un type spécifique de mélangeurs de poudres qui se composent de 2 parties montées sur un arbre central. Le milieu de mélange est souvent constitué de rubans à hélice intérieurs et extérieurs conçus pour déplacer le matériau vers l'intérieur et l'extérieur. Les rubans hélicoïdaux extérieurs tirent le produit des côtés du mélangeur vers le milieu et les rubans intérieurs repoussent le produit vers les côtés. Le mouvement de pliage en va-et-vient des matériaux à mélanger crée un modèle de mélange par convection.
Les rubans sont conçus pour présenter des tolérances d'espacement précises entre les parois du mélangeur. Dans certains cas, ils peuvent même être conçus avec des racleurs de matériaux souples pour empêcher le produit de s'accumuler sur les côtés. Le mécanisme d'entraînement consiste souvent en un entraînement par courroie pour la transmission de la poudre entre le moteur et le réducteur. Cet arrangement utilise un système de courroies et de poulies flexibles pour produire la vitesse et le couple requis pour l'application de mélange spécifique.
Cependant, de plus en plus de fabricants commencent à utiliser des entraînements directs via des moteurs à engrenages qui utilisent un rotor à faible inertie pour s'adapter spécifiquement à la boîte d'engrenages. L'avantage de ce système est qu'il nécessite moins de maintenance pendant toute la durée de vie du mélangeur industriel. Assurez-vous de comprendre la capacité volumique requise pour le mélangeur dont vous avez besoin. Il est essentiel de connaître les densités en vrac des ingrédients à mélanger pour comprendre la capacité requise de votre mélangeur et, surtout, la puissance du moteur nécessaire pour mélanger correctement vos lots. La plupart des mélangeurs de conception standard fonctionnent très bien avec une densité en vrac de 52 kg/m³. Cependant, lorsque vous commencez à mélanger des lots plus denses, vous devez utiliser des moteurs plus puissants et changer les rapports de vitesse.
2. Principaux avantages des mélangeurs à ruban
Les mélangeurs à ruban constituent l’équipement de mélange industriel le plus polyvalent. Ils sont souvent utilisés pour le mélange entre solides, mais peuvent également être utilisés pour des applications impliquant l'enrobage d'une particule sèche avec un ingrédient liquide, ou même l'absorption par la particule d'un ajout de liquide. Des applications plus rares permettent de réaliser des mélanges de suspension de boue et de particules liquides, nécessitant une conception particulière.
Grâce au mode de mélange par convection du mélangeur à ruban, des cycles de mélange courts et rapides sont possibles, allant souvent de quelques minutes à 20 minutes (selon le volume et la complexité de la formule). Compte tenu des cycles de mélange rapides de ces mélangeurs de solides en vrac, on pourrait penser que les rubans tournent à un régime très élevé, mais ce n'est pas le cas.
Les agitateurs de rubans ne fonctionnent généralement pas à une vitesse supérieure à 1,5 m/s. Cette faible vitesse crée une action de pliage en douceur des particules à mélanger. Par conséquent, cela permet une utilisation sur des matériaux fragiles et friables tout en préservant l'intégrité des particules.
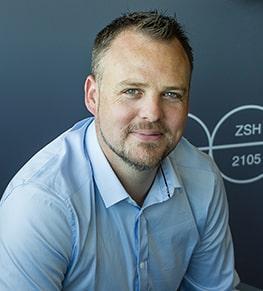
Vous avez un projet ? Je suis disponible pour vous
conseiller et vous accompagner dans votre étude.
Erwan Guillard, expert poudre
Les mélangeurs à ruban sont également capables de se décharger complètement via un orifice de décharge situé au centre. En faisant fonctionner le mélangeur à basse vitesse, le produit peut être facilement poussé d'avant en arrière jusqu'à ce que le récipient de mélange soit presque vide. Diverses vannes à poudre peuvent être utilisées sur l'orifice de décharge du mélangeur, mais les plus courantes sont les vannes à bouchon. Les vannes à boisseau offrent l'avantage de se trouver au même niveau que la surface interne du corps du mélangeur lorsqu'elles sont en position fermée, ce qui empêche l'accumulation de matériau pendant le cycle de mélange. Les capacités de volume de travail d'un mélangeur à ruban sont souvent inférieures à 30 % de sa capacité, toute valeur inférieure ne permettant pas un contact suffisant entre les rubans et les matériaux à mélanger. Dans certaines applications, le mélangeur peut fonctionner à près de 100 % de sa capacité, mais souvent, la capacité de mélange optimale se situe autour de 50-70 % du volume.
Grâce à leur polyvalence et à leur action de mélange en douceur, les mélangeurs à ruban ont une longue liste d'applications parmi lesquels on peut citer les épices, les plats préparés, les mélanges de boissons, les produits nutraceutiques, les cosmétiques, les polymères et les composés plastiques, les engrais et les céramiques... Ils peuvent être utilisés dans n'importe quelle industrie traitant des matières sèches telles que : l'alimentation et les boissons, la pharmacie, la chimie, les minéraux et l'énergie.
3. Paramètres à prendre en compte
Une chose importante à prendre en considération lors de la conception d'un mélangeur à ruban pour votre process est l'utilisation d'un entraînement à fréquence variable. Un variateur de fréquence permet un démarrage en douceur et réduit l'usure des mécanismes d'entraînement lors du lancement du processus de mélange à pleine charge. Les démarreurs Delta, ou démarreurs progressifs électroniques, peuvent également être intégrés aux commandes pour accomplir la même tâche, mais ils ne sont destinés qu'aux entraînements à vitesse unique.
Un autre élément à prendre en compte est la finition de la surface interne du corps du mélangeur et des agitateurs. Si vous travaillez avec un lot de produits mélangés à écoulement assez fluide, votre finition standard par projection de billes de 80 grains fera l'affaire. Mais pour les applications sanitaires, ou les matériaux qui ont tendance à s'accumuler et à coller aux surfaces, des finitions de 150 grains peuvent être plus appropriées. Un polissage miroir peut même être nécessaire pour faciliter le nettoyage de l'équipement et éviter la contamination croisée entre les lots. Pour éviter davantage la contamination croisée, votre fournisseur doit pouvoir concevoir un mélangeur avec un agitateur facilement amovible pour le nettoyer et permettre un meilleur accès au corps interne du mélangeur lui-même.
Des hachoirs (également appelés disperseurs) peuvent également être intégrés au support du mélangeur. Il s'agit de lames à rotation rapide qui aident à briser les matériaux qui ont tendance à adhérer à eux-mêmes et à former des amas.
Pour les mélanges discontinus contenant des matériaux abrasifs, tels que les poudres céramiques, un revêtement Hardox peut être appliqué aux surfaces internes pour une meilleure résistance à l'usure. D'autres options à envisager pour l'intégration sont des dispositifs d'échantillonnage pour prélever des échantillons en temps réel pendant le mélange, des enveloppes de chauffage/refroidissement pour contrôler les températures du mélange, et des purges de nitrogrène pour inerter les matériaux combustibles.
Afin de décider quel mélangeur est le mieux adapté à votre procédé, contactez l'un de nos experts.